Our Services
We offer a variety of servies as well as a comprehensive training programme in preparation for JUKI’s SMT manufacturing solutions at our headquarters situated in Nuremberg, Germany. Our offer ranges from demos in our demo centre to product specific training, special training packages and service stipulations as well as consultation free of charge regarding special requirements (nozzle, special components, tact time determination). If requested, it is possible for you to receive a customized training where our experts will even come by on-site to your company. When necessary a team of technical experts is onhand around the clock to offer support.
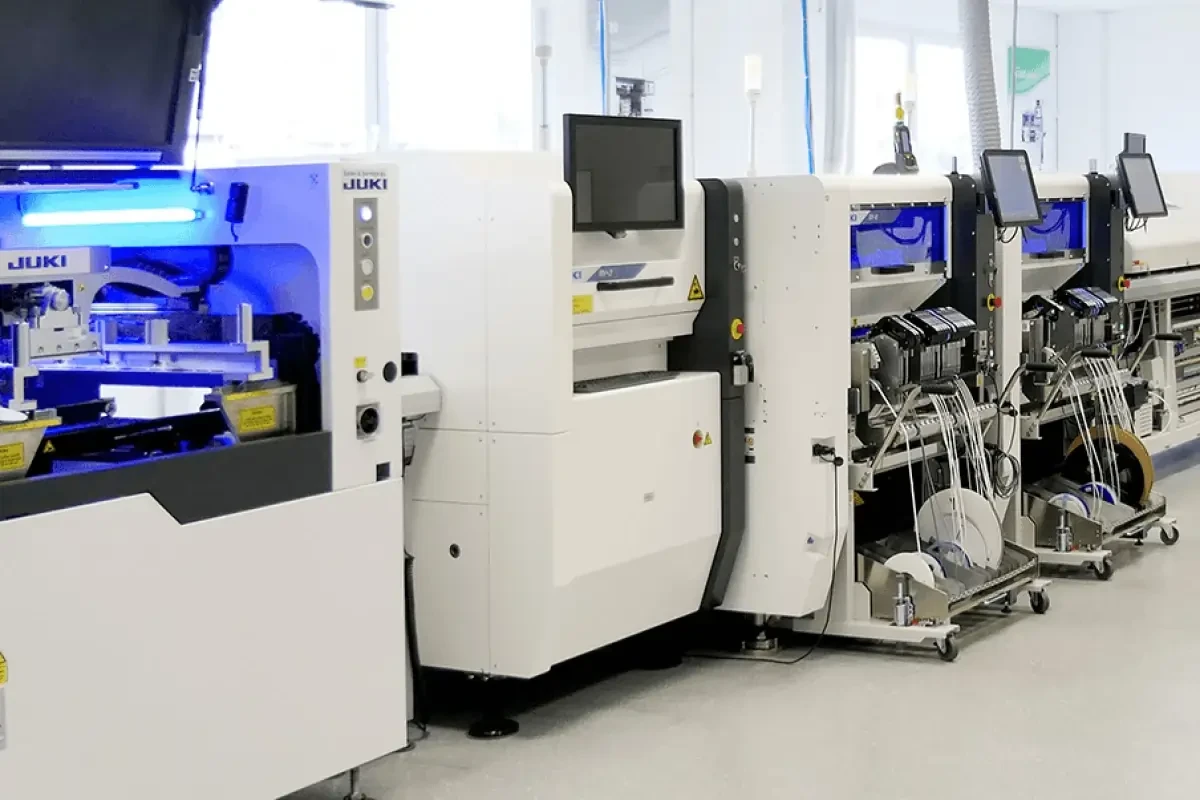
Democenter
Explore Our Products at the JUKI Demo Centre in Nuremberg, Germany
Are you eager to delve deeper into our product offerings?
Join us at the JUKI Demo Centre, conveniently located at our European headquarters in Nuremberg, Germany. Immerse yourself in a firsthand experience of our state-of-the-art SMT assembly line, and witness the performance spectrum and reliability of our JUKI products.
Spanning across 500 square meters, our exhibit showcases the latest additions to our extensive product portfolio.
Our knowledgeable experts are dedicated to understanding your unique requirements, tailoring the demo to meet your specific needs.
As a gesture of appreciation for your time, we invite you to indulge in some delectable snacks at our customer lounge following the demo.
Schedule an appointment today with your dedicated contact partner from our sales department for a personalized demo experience.
We eagerly anticipate your visit!
Training Center
Elevate Your Success with JUKI Training Programs!
Are you already utilizing JUKI products? Seize the opportunity to enhance your skills and empower your team in mastering the operation of our machines and comprehensive solutions!
Benefit from our seasoned coaches with extensive experience, dedicated to optimizing individual processes and driving long-term enhancements across your production line. Our offerings include:
- Professional Expertise: Tap into the wealth of knowledge provided by our experts.
- Practical Relevance: Gain insights directly applicable to real-world scenarios.
- Personal Engagement: Receive tailored guidance and support to meet your unique requirements.
Choose from a diverse range of topics, spanning fundamental seminars, programming and maintenance training, and specialized courses—all customized to suit your team's training needs and existing knowledge levels.
With two spacious training rooms, each accommodating up to eight participants, we ensure an immersive and interactive learning environment.
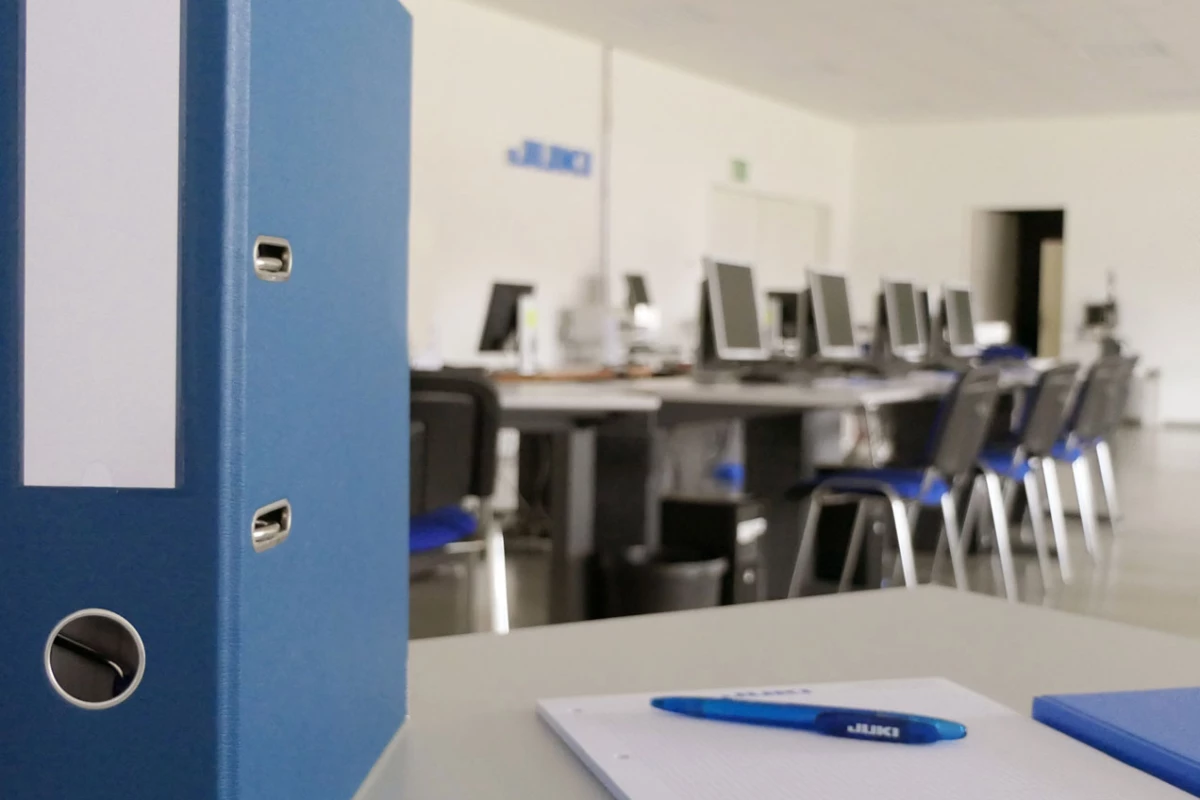
Training Packages
Choose from a variety of topics, including foundational seminars, programming and maintenance training, and specialized courses—all customized to meet the specific training needs and knowledge levels of your employees.
Unlock the Full Potential of JUKI SMT Assembly Solutions with Our Comprehensive Training Package!
Embark on your journey into the world of JUKI SMT assembly solutions with our all-inclusive care package designed specifically for new clients. Our training offering provides a structured curriculum aimed at equipping you with essential skills for proficiently handling and programming JUKI products, enabling you to streamline your operations and enhance productivity.
Key highlights of the course include:
- Hands-on training in handling and basic programming setup of JUKI Pick and Place machines.
- In-depth instruction on programming techniques tailored for JUKI Pick and Place machines.
- Guidance on converting CAD data for seamless integration with JUKI Pick and Place machines.
- Comprehensive training on the operation and programming of Intelligent Feeder Systems.
Expand Your Team's Expertise with JUKI SMT Assembly Solutions Training for Existing Customers
Discover our extensive array of training options tailored specifically for existing customers, aimed at enhancing the proficiency of employees in managing JUKI SMT assembly solutions. Our training programs are meticulously curated to meet the unique needs of operators and programmers, offering a comprehensive selection divided into specific product categories for targeted learning.
Key features of our training include:
- Fundamental training for operators and programmers to establish a strong foundation.
- Advanced fundamentals tailored specifically for programmers to deepen their expertise.
- In-depth exploration of options and functions for subsequent and intensified applications.
- Comprehensive instruction on maintenance practices to ensure optimal performance.
Tailored Training Solutions for Your Needs and JUKI Products
We provide customized training solutions to address your specific requirements and the JUKI products utilized in your production. Our experienced coaches can arrange personalized sessions tailored to your topical focus areas, desired comprehensiveness, and preferred duration.
Training sessions are typically conducted at our facilities in Nuremberg, Germany. Alternatively, we can accommodate on-site training at your company's location upon request.
Practical Training with Hands-On Support
Our training courses are renowned for their practical relevance, ensuring that participants gain valuable hands-on experience. In addition, we offer the option to enhance training sessions under special circumstances. This includes providing specific process support or organizing professional practice days focused on specialized topics such as components and programming.
If you have any inquiries about our training packages or require more detailed information, feel free to reach out to us at vp.training@ml.juki.com.
We are here to assist you!
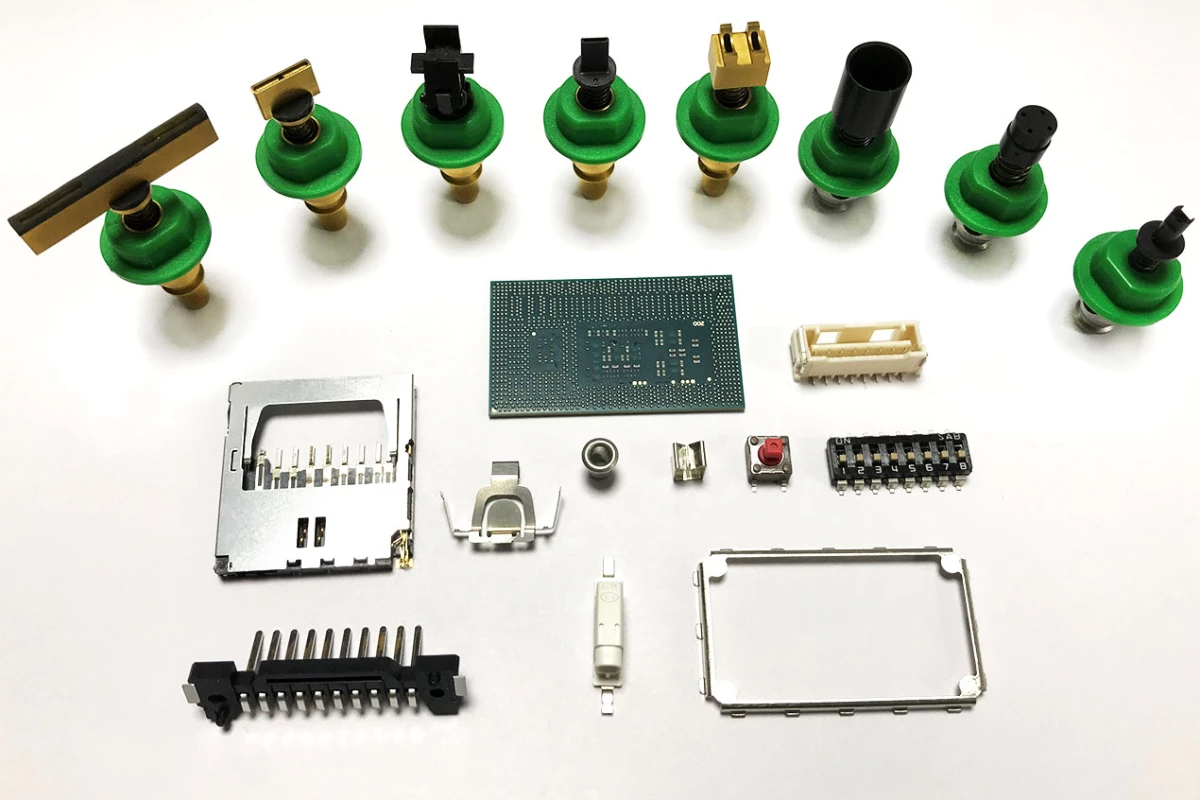
Applications
The Application team handles your specific requests on:
- Selecting the appropriate nozzle for unique components
- Custom nozzle production for intricate component shapes
- Assistance in defining vision and laser components
- Tact time assessment for JUKI Pick and Place machines
Contact your dedicated sales representative to discuss your requirements and the next steps toward implementation.
We're ready to tackle your challenges!
Material-Flow-Analysis
Effective storage management directly influences material flow and impacts company costs and revenue. Optimizing your warehouse presents opportunities while mitigating risks. We're here to assist you in identifying improvement potentials. Take advantage of our free warehouse analysis to streamline operations and reduce costs. Explore simple yet impactful optimization strategies to enhance material flow efficiency.
We're here to help you uncover areas for improvement and provide a complimentary warehouse analysis.
Explore easy-to-implement optimization strategies to enhance material flow and streamline operations.
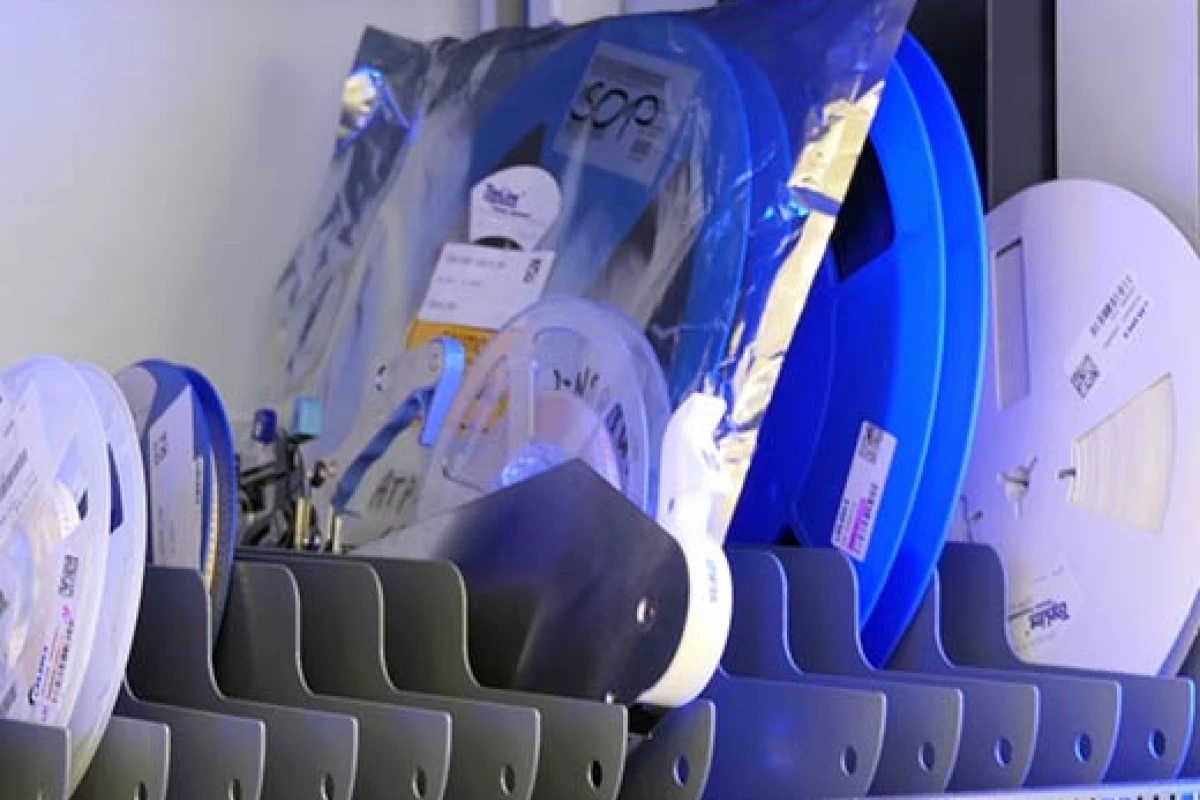
JUKI SmartCare
Relax – the line is running! Ensure smooth operations with our SmartCare maintenance contract! Our expert team works tirelessly to boost system availability and enhance production quality, all at predictable costs.
The components of our JUKI SmartCare maintenance concept include:
- Annual machine maintenance
- Comprehensive functional checks
- Prompt minor repairs (within 1 hour)
- SmartCare status report generation
Additional details:
- JUKI SmartCare available for various machine types and generations
- Utilization of original spare parts packages
- Same-day spare parts delivery (orders placed by 2 p.m.)
- 48-hour response time (orders received by 4 p.m.)
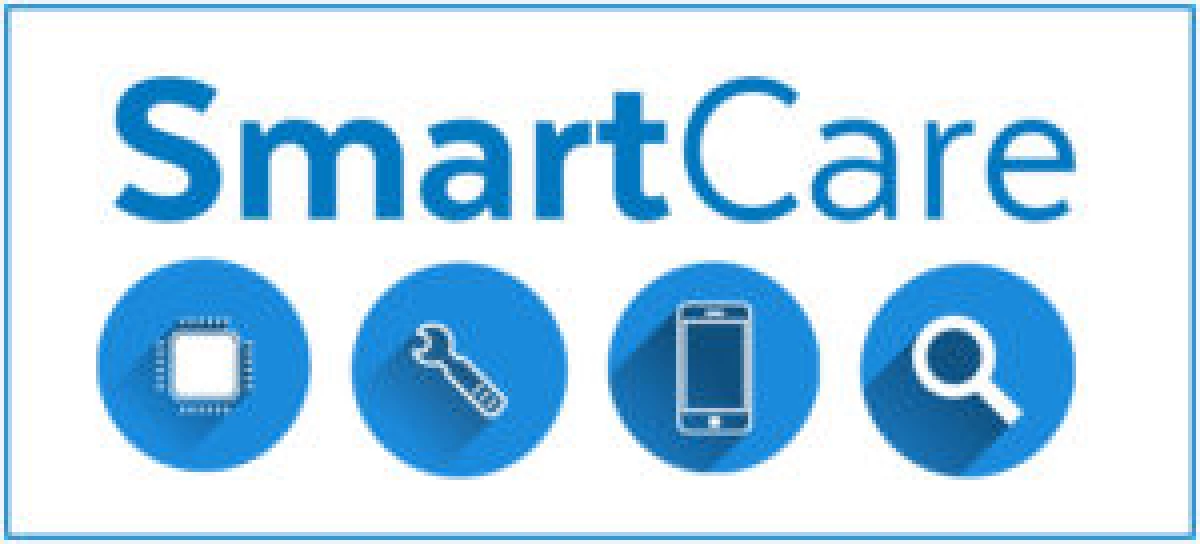
JUKI Detect
Experience technical issues? With JUKI Detect, our expert team offers immediate remote support to keep your production line running smoothly. Our innovative features include:
Our innovative features of JUKI SmartCare include:
- Error diagnosis via video call (computer to mobile device)
- Augmented reality for 3D markings directly on your machine
- Real-time file transfer (e.g., software updates)
- Logging for future analysis
Benefits at a glance:
- Elimination of travel expenses and hotel costs
- High availability and fast reaction time
- Video logging and efficient video-based communication
Count on JUKI Detect for seamless production continuity!
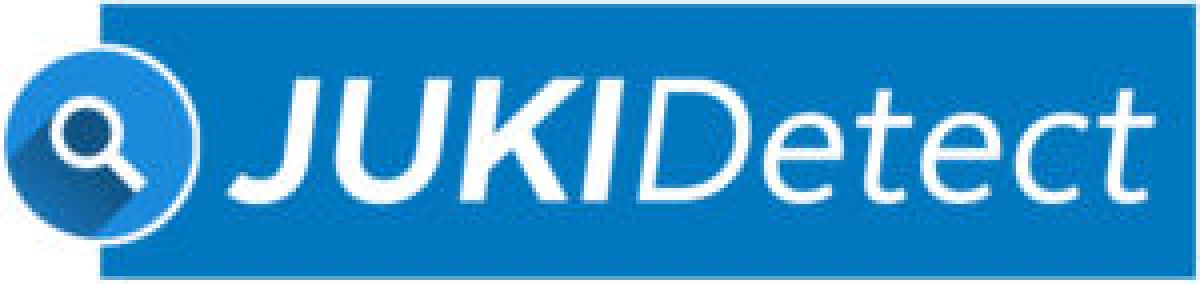
Technical Service
For technical inquiries, reach out to our service team via email anytime. For urgent machine failures, call our 24-hour service hotline at any time. Our technical experts are ready to assist you promptly.
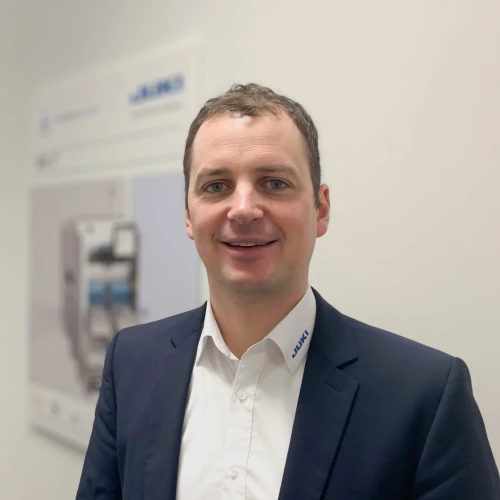